Our advanced recycling technology
Styrenyx
Advanced recycling technology that uses catalyst-free depolymerization to recycle polystyrene waste back to its virgin-equivalent building blocks for reuse in new, high-quality products.
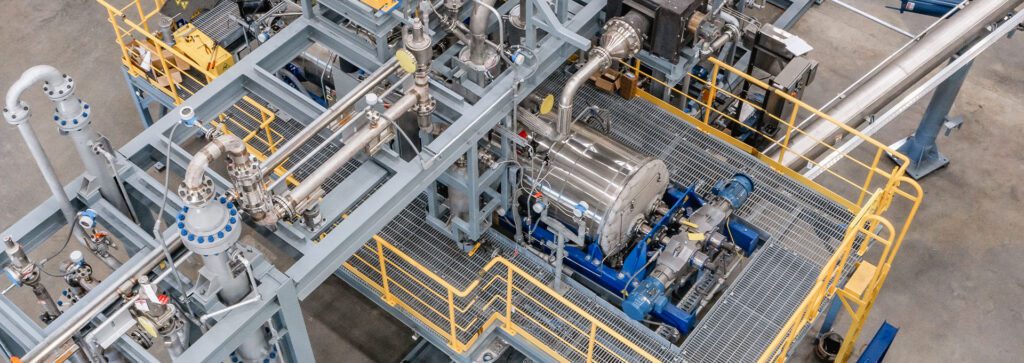
Preserving the value of plastic, sustainably
Agilyx’s advanced recycling technology tackles the global plastic waste problem by processing hard-to-recycle plastics that traditional recycling methods cannot. Styrenyx, our proprietary depolymerization process, uses controlled temperatures to break polystyrene into its original building blocks, preserving their value for continuous reuse in a circular economy. Our technology supports a sustainable future by using an electrified reactor with lower carbon impact and a renewable energy source.
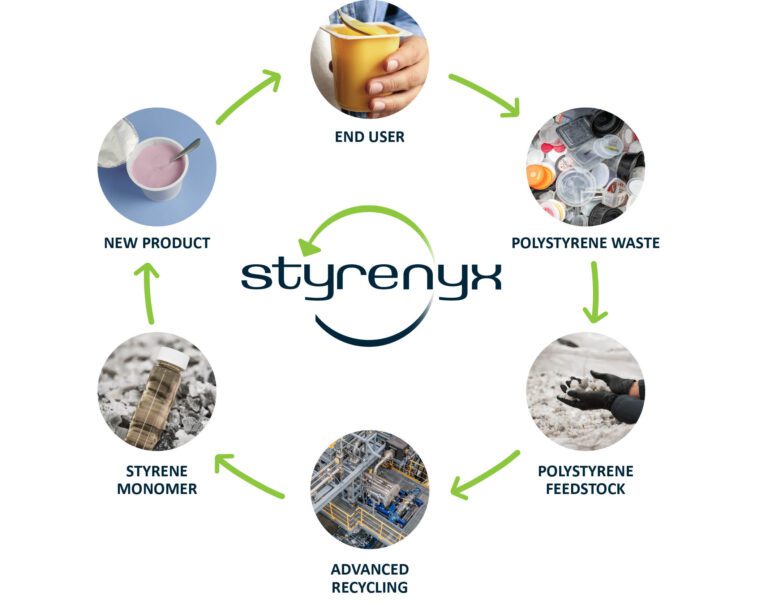
Our technology can reduce carbon equivalent emissions for styrene production by up to 86% compared to fossil-based production
Agilyx commissioned Sphera Solutions to conduct a cradle-to-gate carbon footprint assessment revealing that Styrenyx:

Cuts CO₂ emissions by 38% using grid electricity

Lowers emissions by 86% when
powered by wind energy

Could remove the equivalent of 325,000 gasoline cars from the road annually if applied to just 10% of global styrene production
Built for versatility Styrenyx is used in commercial-scale technology platforms to redirect plastic waste from the landfill and back into use. Unlike other technologies, Styrenyx’s reactor does not use a catalyst. This means we are able to process contaminated plastic waste, greatly increasing recyclability rates.
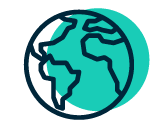
Lower-carbon process
Reduces carbon impact by using an electrified reactor powered by a renewable energy source
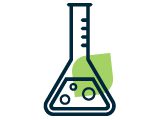
Catalyst-free system
Allows contaminated polystyrene feedstocks

Robust feedstock capability
Allows input of a broad range of polystyrene feedstocks and blends (including, waste PS, GPPS, EPS, XPS, HIPS, ABS, AS & SAN)

Flexible process
Reduces carbon impact by using an electrified reactor powered by a renewable energy source
Backed by 20+ years of technology development
With eight generations of technology development, a robust portfolio of patents and a license actively operating at a waste polystyrene recycling facility in Japan, Agilyx has established its leadership position in the advanced recycling industry. The technology is compatible with ISCC PLUS certification standards, enabling traceability and verification of recycled content to support customer and regulatory requirements.
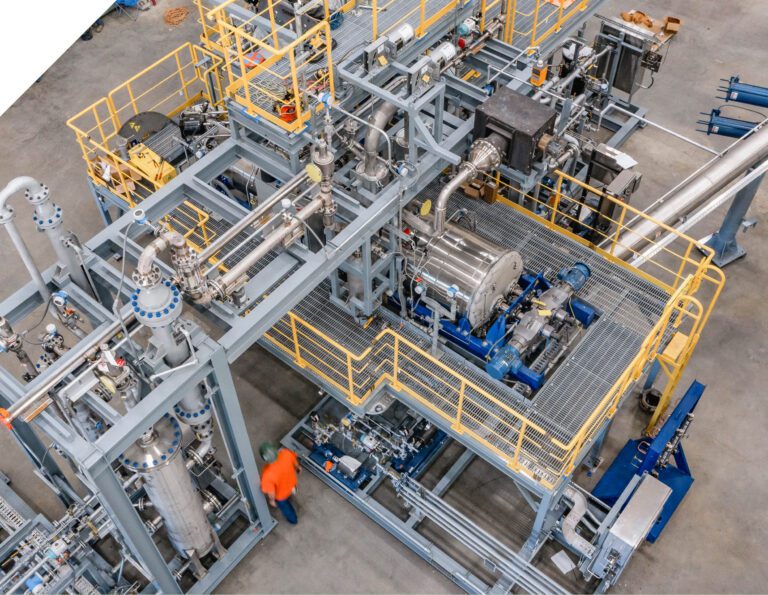
Styrenyx: Feedstock to Product
Styrenyx is designed to drive the future of sustainable packaging by enabling plastics to be recycled repeatedly, reducing reliance on fossil-based materials and significantly lowering carbon footprints.
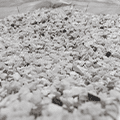
Input: Polystyrene feedstock
Densified polystyrene waste is fed into the reactors.
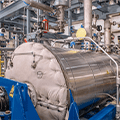
Conversion: Depolymerization
Our patented pyrolysis reactor depolymerizes, (breaks down using high, controlled temperatures) the polystyrene into its original building blocks: styrene monomers.
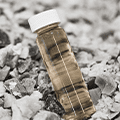
Output: Styrene monomer
The end-product, a styrene monomer, enables all styrene monomer end-markets to create new, virgin-equivalent, high-quality polystyrene products, displacing the need for fossil-based production.
Styrenyx is proven on a commercial scale
Styrenyx is at the heart of Toyo Styrene’s advanced recycling facility in Chiba, Japan — the largest facility dedicated to the depolymerization of polystyrene waste in the country.
This innovative facility converts polystyrene waste into a styrene monomer using Styrenyx technology. The recovered styrene monomer can be used in making high-quality polystyrene products with a significantly reduced carbon footprint compared to those made with virgin materials.
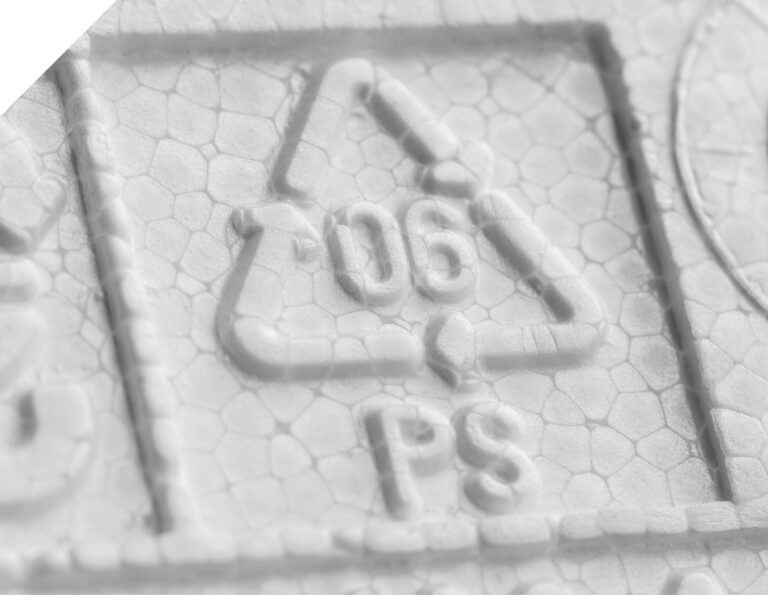